Inside our QC process
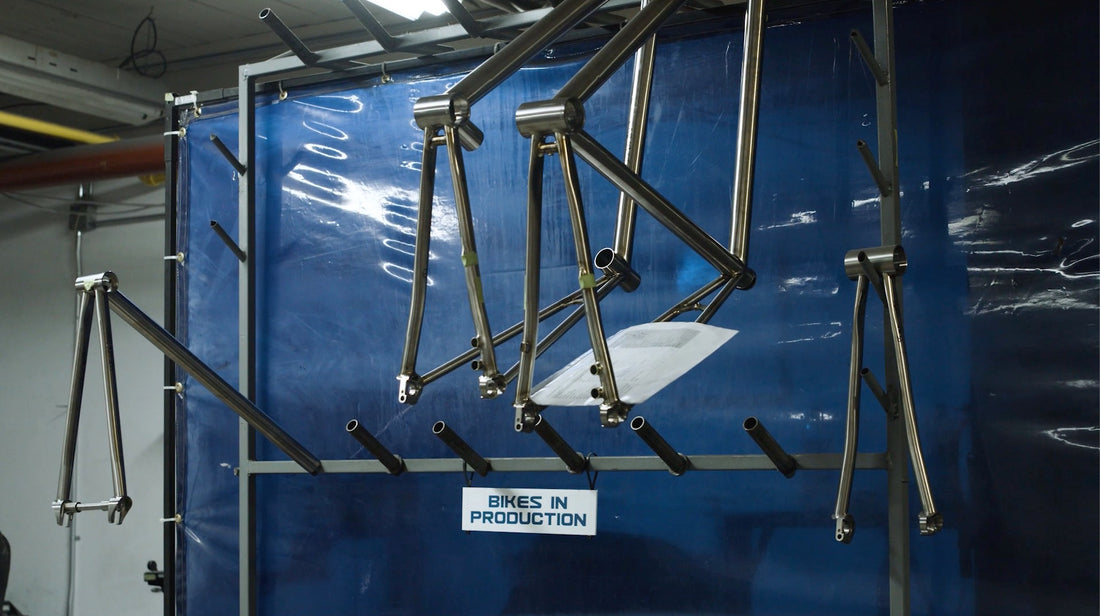
In 2014, Dries moved halfway across the country to work on No. 22 bikes, where he’s been gaining experience as a welder while taking care of the quality-control and the final machining phase on each frame. Immediately after the bike is through the weld shop, it comes to Sam.
“After a bike is welded, it’s actually not yet rideable, but it looks like it should be,” Dries points out. “The distortion of the heat from welding means the threading won’t work. You couldn’t press a headset in or thread a bottom bracket in to it; you don’t see it, but it’s got to be done.”
First, Dries performs an alignment check on the frame. Then the seatpost insert gets bonded in. After that, he chases the threads in the bottom bracket, reams the head tube so that the headset will press in, verifies that the derailleur hanger is aligned correctly, and checks any braze-ons and their threading for bolts. “This phase is all about making sure every detail will come together nicely when you do the final build,” he says.

Once a bike is done with QC and final machining, "if you wanted to you could hang parts on it and ride it out the door, “ Dries says. “This final effort is all about what you don’t notice or might take for granted in a build. It’s about making it a rideable bike—from “OK” to nicely polished."
Dries’ long-term goal is to become a full-time welder as well. “[Head welder] Frank is a tough act to follow,” Dries says. “I’ve seen a lot of good welders, and Frank’s welds can stand up to anybody’s.” Dries has spent the past couple of years refining his welding chops, doing welds on some front ends of frames, and he now handles most of the tacking—welding the seat tube and not fully welding the front end, but putting it together on the alignment plate.
“For the most part, everything is one bike at a time,” Dries says of the process. “Every bike gets a lot of individual attention.”
Dries’ favourite build is the Drifter. “That’s because of my riding style—that model fits it perfectly,” he says. Dries also owns a Broken Arrow and a very early prototype of our mountain bike. “But it's not an official Old King,” he jokes. “I’m about 80% done welding another Broken Arrow for myself, it’s part welding practice and a B-bike for cross season. I still race cross from time to time.”