
One of the defining characteristics of No. 22 is that we are continuously searching for innovations and improvements to our frame designs, down to the smallest components that go into them. While readily available ‘off the shelf’ solutions are often the easiest solution, they’re limited and do not allow us to make No. 22 the unique and innovative brand we want it to be. A great example of this approach is in the dropouts on each of our bikes.
One of the most crucial components on a bike, the rear dropouts determine the size and shape limitations of the rear triangle tubes, connect the drivetrain to the wheel and in many cases impact the performance of your bike’s shifting.
General Approach
Crisp handling and response to pedalling forces is a key design goal of all of our bikes. One of the ways that we achieve this is by providing the largest surface area to weld the chainstays and seatstays to the dropout, providing the stiffest and strongest possible connection. This is why all of our bikes utilize hooded dropouts instead of commonly seen “bullet” style dropouts.

The most economical way of fabricating a hooded dropout is by welding the hood to the axle plate. We don’t do that: we machine our track dropouts from a solid billet of 6Al-4V Grade 5 titanium (the hardest Ti alloy used on bike frames). This eliminates the potential for failure or heat distortion at the weld that would connect the two halves of the drop-out and makes for a stiffer, cleaner component.
To illustrate how we feel we’ve improved over the status quo, a review of each dropout from simplest to most complex is a great insight into our design process.
Little Wing | Track Dropout
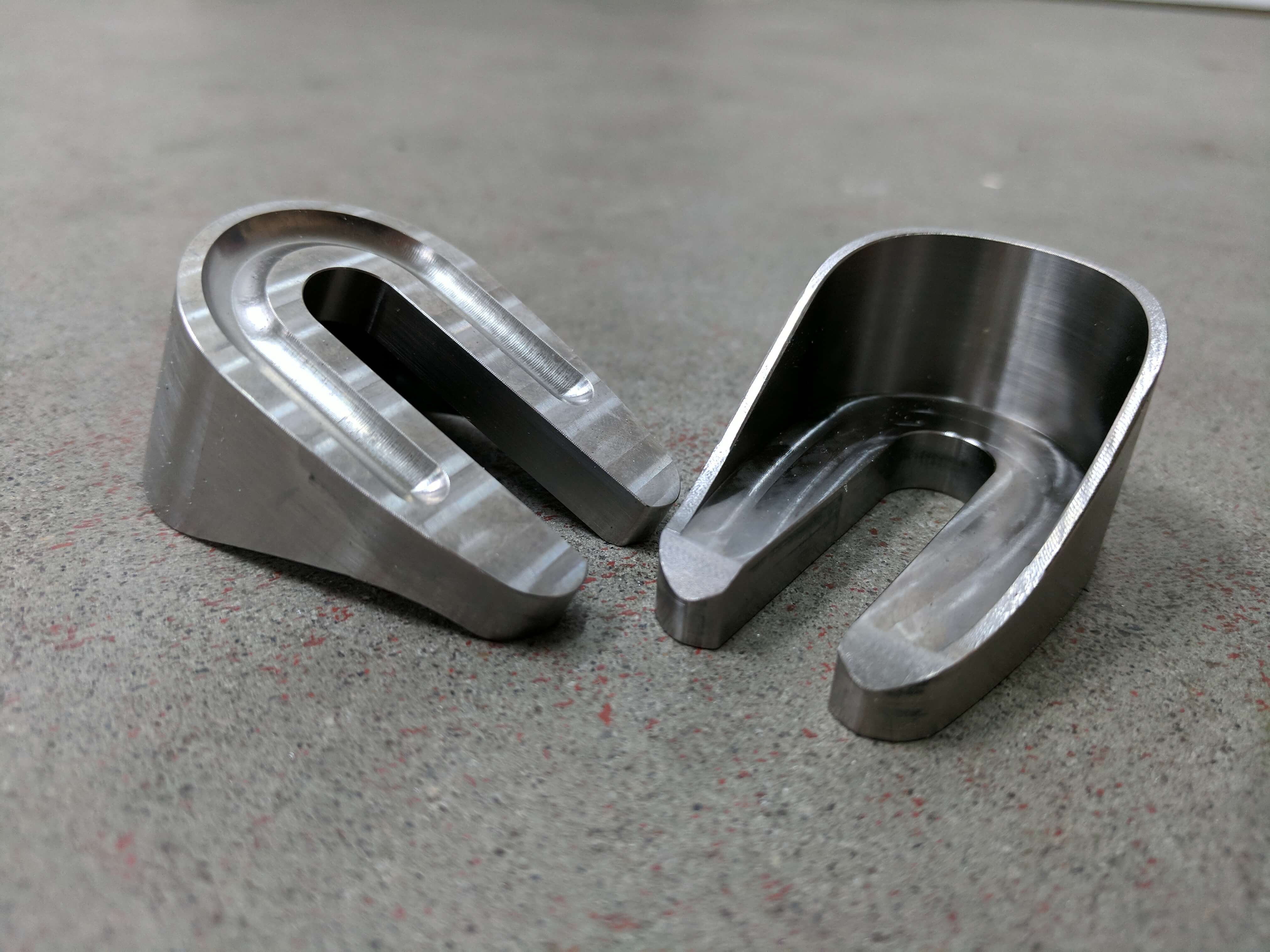
A track specific dropout is the most basic iteration of the component. Without the need to accommodate a derailleur, the mandate here is to provide a robust interface that can accommodate large seat and chain stays to provide the needed power transfer under explosive sprint efforts. Our solid, hooded track dropout is the best way to achieve this goal.
Our track dropouts use an extra long 1” axle slot. This long slot allows for ample room to adjust chain tension, and also allows for gearing changes without always needing to add or remove chain links. A key feature for riders making frequent gearing changes between track events or switching from mid-week courier gearing to weekend track ride gearing.
Great Divide | Road Dropout
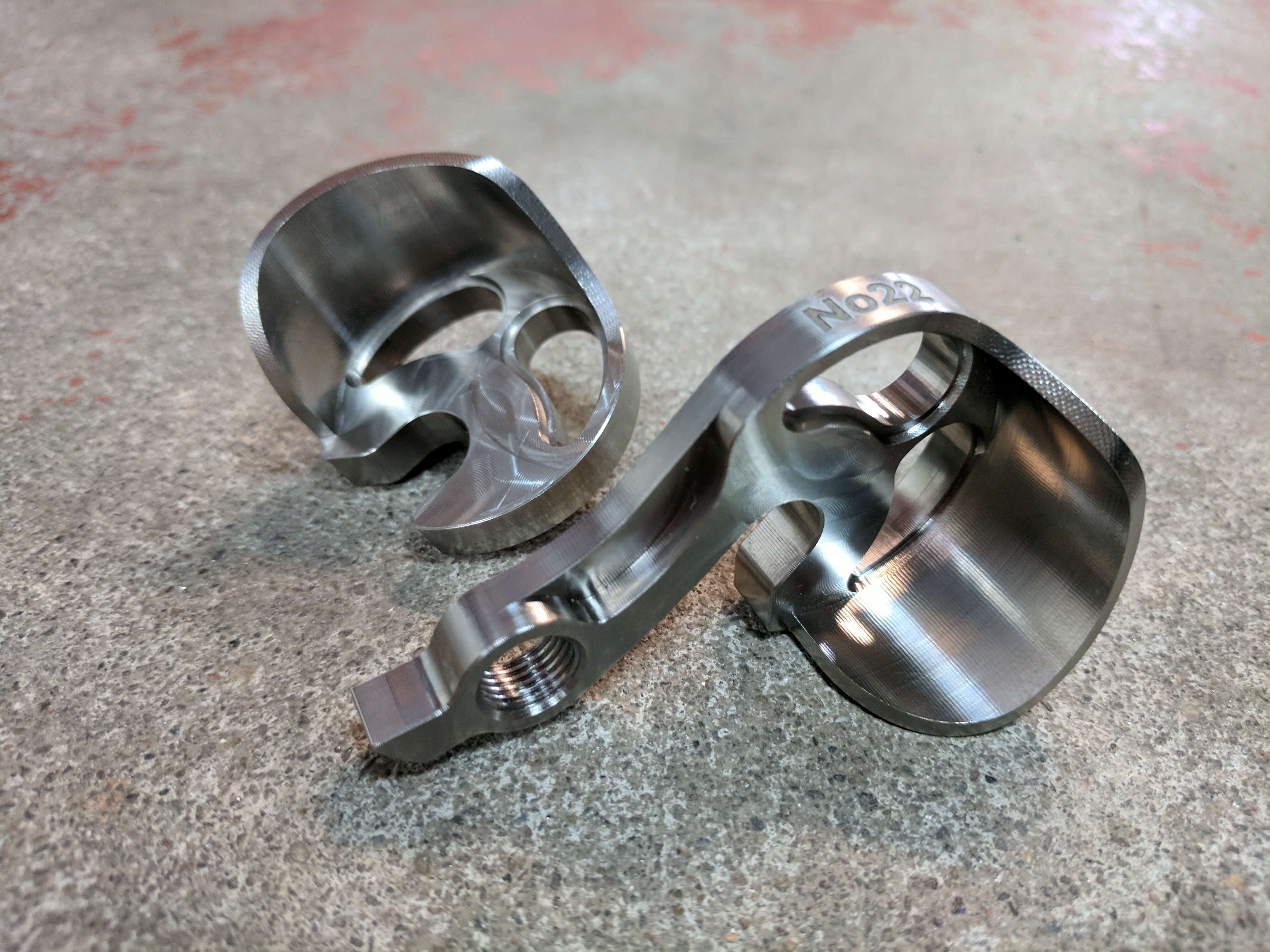
As with all our dropouts, the Great Divide’s quick release dropouts are machined from a solid billet of 6Al-4V Grade 5 titanium. There are three unique features of our quick release road dropouts to note:
Our dropout uses an integrated titanium hanger instead of a bolt-on aluminum hanger. This allows for far more precise derailleur alignment, keeping your drivetrain shifting better for longer, and adds substantial stiffness compared to a conventional replaceable hanger. This stiffness is most noticeable with electronic drivetrains, where the huge lateral loads of shifting electronic derailleurs can visibly deflect softer aluminum hangers.
While an integrated hanger seems like a simple solution, the larger dimensions of the dropout mean that it can no longer be made from machining a bar of titanium as most dropouts are. Instead, the bigger dimensions of the integrated hanger require the dropout to be machined from a single large billet of titanium. The material and machining costs of this approach are roughly double that of a smaller dropout with a replaceable hanger, but the result is a stiff, strong and beautifully sculpted piece.
On the subject of the sculptural element of the dropout, we use a unique double relief design that adds aesthetic elegance while shaving unnecessary grams.
The hood width of the dropouts allows us to connect a large 22mm chainstay with ample room to weld the entire way around the tube. This reduces the possibility of failures that can occur when too much of a weld runs over the edge of the connected materials, weakening the connection.
Finally, while a small point, using our own dropouts allows for subtle branding of the drive-side dropout. While not a performance benefit, it’s a reflection of the unique attention that goes into each component of our bikes.
Reactor | Road Race Dropout
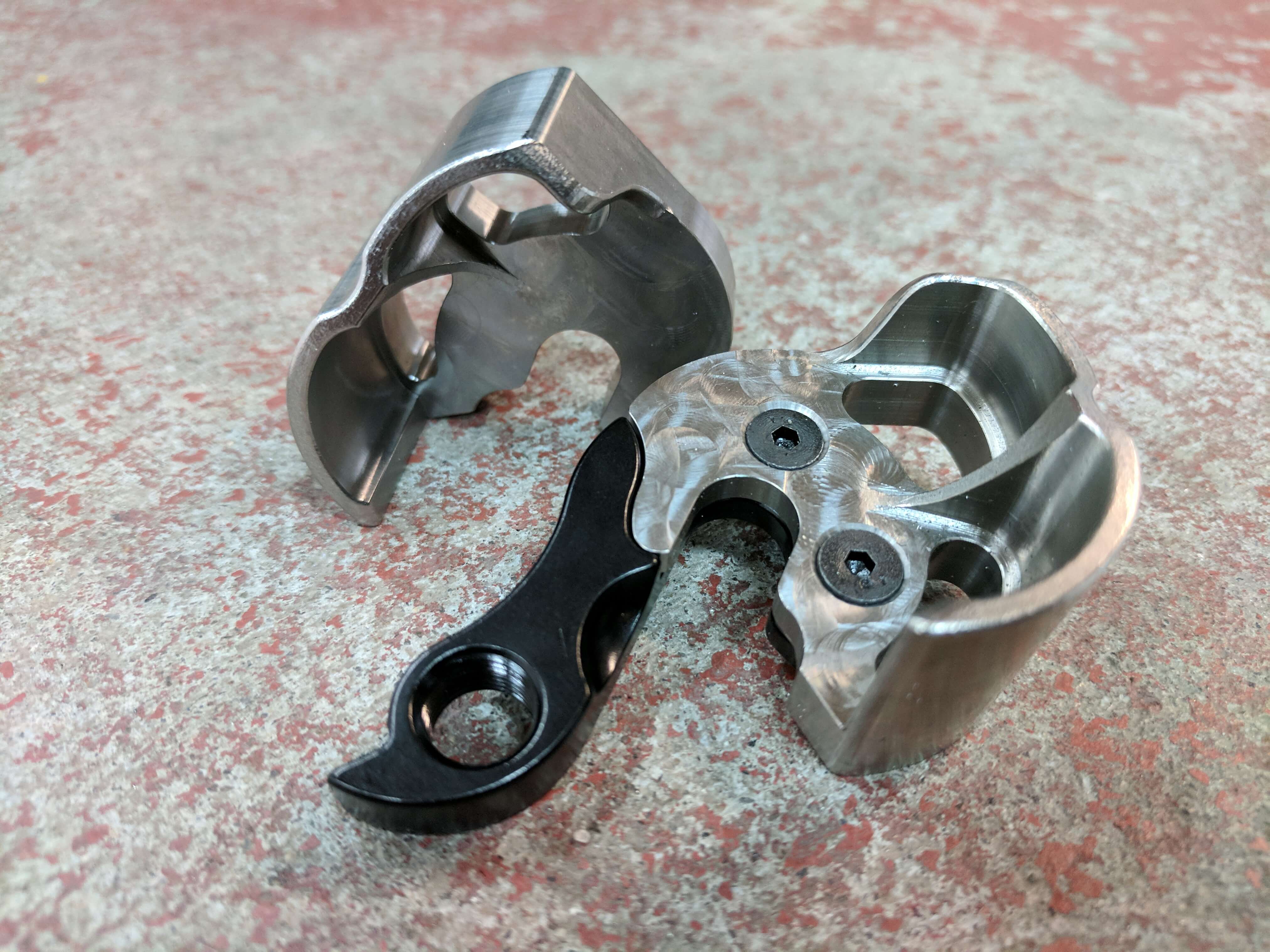
The Reactor is the only titanium road race frame that we know of that uses massive 1” chainstays for rear end stiffness rivalling modern carbon race bikes. This is likely due to the fact that there is no readily available dropout that can accommodate these oversized chainstays.
As the dropout needs to be quite large on the Reactor, these dropouts are aggressively relieved in a number of locations to shave grams off this weight sensitive frame without sacrificing the structural integrity of the dropouts.
Compared to our Great Divide dropouts, the Reactor dropout uses an extra thick replaceable aluminum hanger instead of an integrated titanium hanger. The replaceable hanger found a home on the Reactor given the Reactor’s more race focused mission, and the crashes and abuse that goes along with this more aggressive use.
All Disc Models | Thru-Axle Dropout
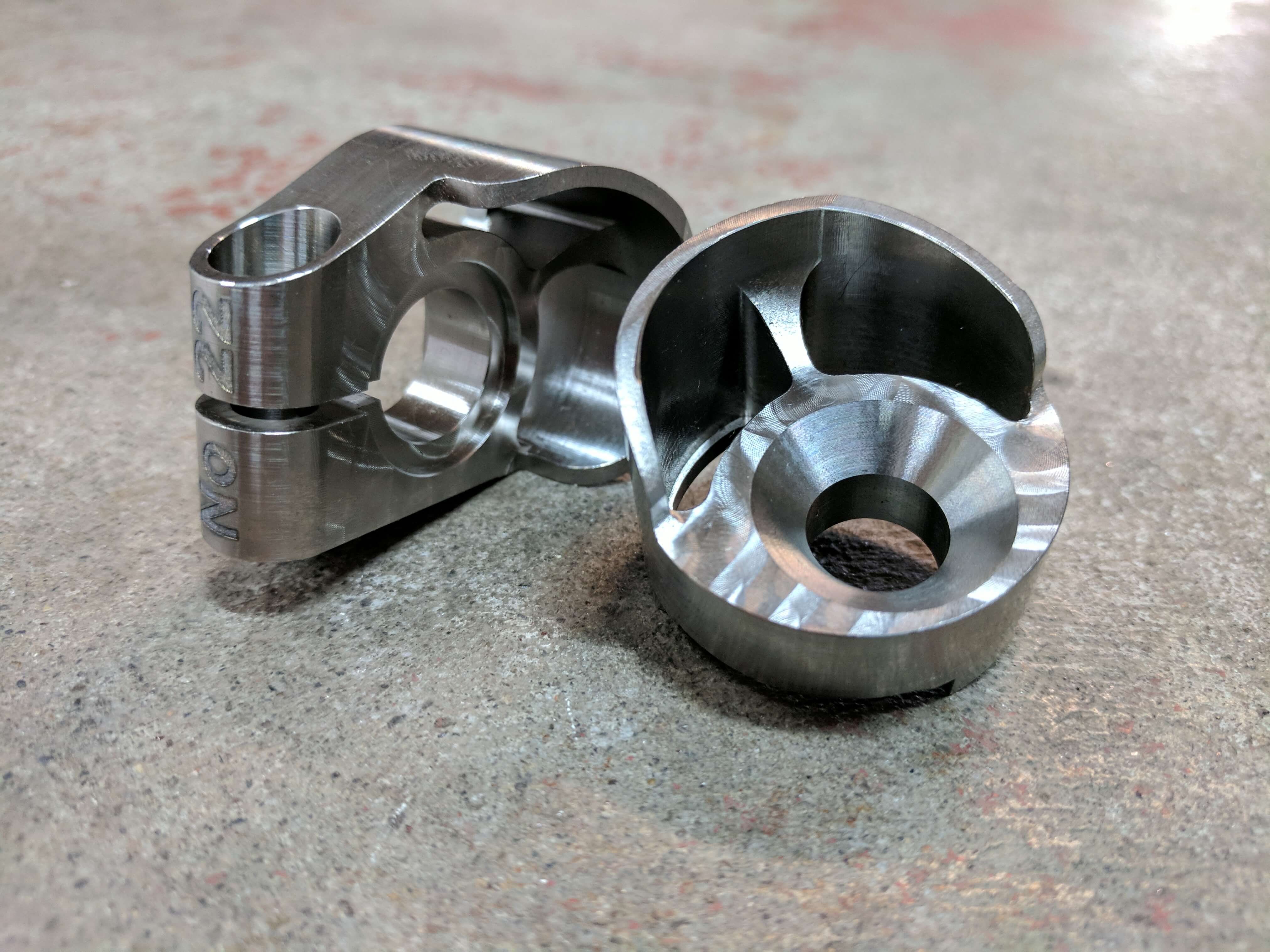
As disc brakes have become more and more popular throughout our lineup, we were sent searching for a versatile thru-axle solution for use on our growing number of disc brake models. With several key advantages over other systems, we designed our thru-axle disc dropouts around the clever Syntace X-12 system.
The Syntace system takes a unique approach to a replaceable derailleur hanger. Unlike many replaceable derailleur hangers which are soft enough to bend or break easily, the Syntace hangers are stiff and robust. Cleverly, the hanger attaches to the frame with a hollow breakaway bolt which is intended to shear in an impact. This leaves the aluminum hanger stiff enough to handle high shift loads, but protects the derailleur from large impacts and makes trailside repairs as simple as replacing a single bolt.
The hangers are also offered in a variety of designs allowing for us to adapt to direct mount standards which while long-standing in MTB, have only recently started to make their way into road groupsets.
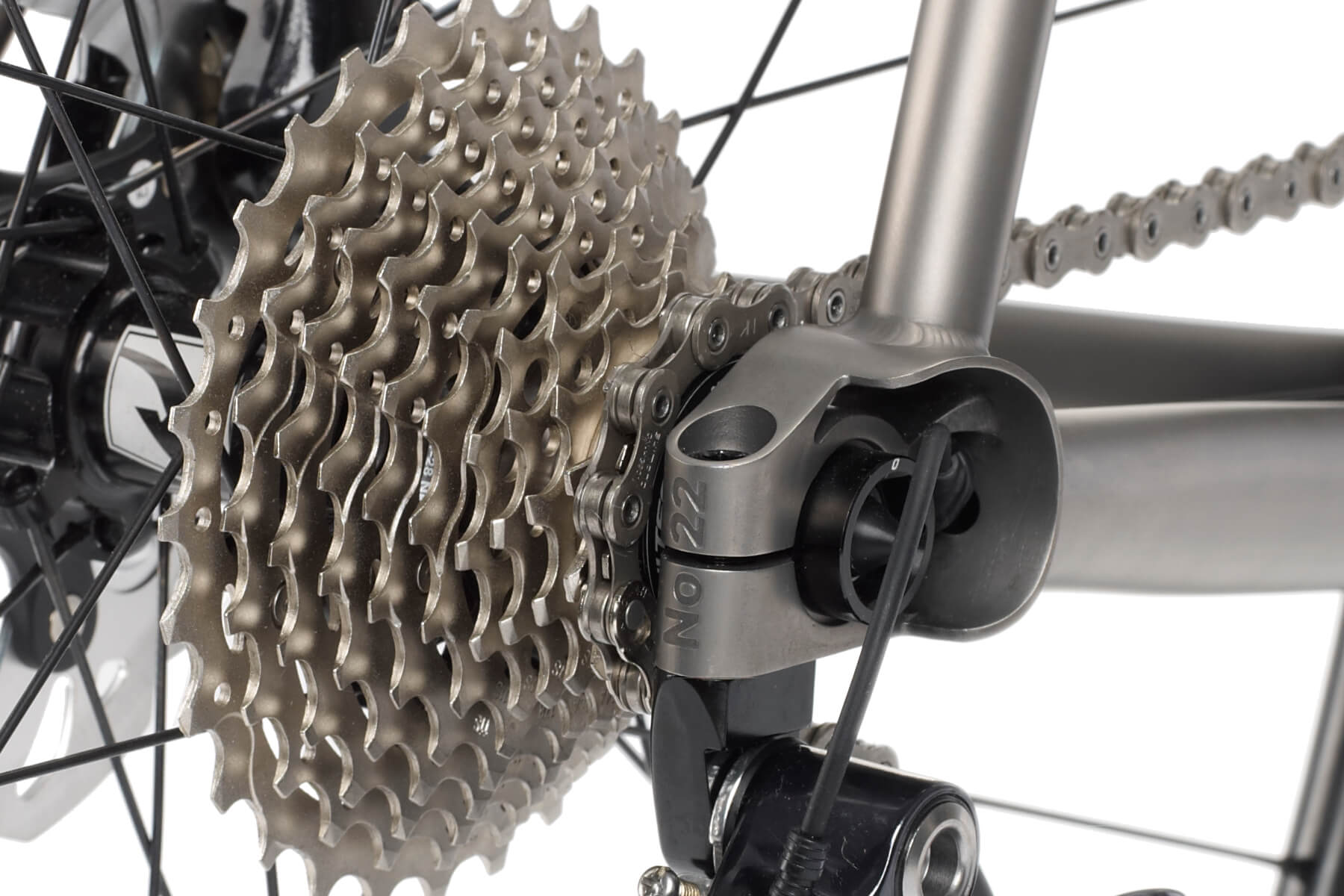
The Syntace X-12 system also proved to be a perfect solution to meet the requirements for flat mount disc brake calipers. Having just completed a design for our thru-axle drop-outs, the details on flat mount were released and it was back to the drawing board. The relationship between the center of the axle and the top of the flat mount boss is key to proper brake pad placement and alignment. We revised the design of our dropouts to be one of the first companies to offer our disc models with flat mount calipers front and rear.
To add our personal touch to our disc dropouts, similar to the Great Divide a time- and cost-heavy double relief design is used to save weight, topped off with subtle branding on the drive side.
Have a question for us about our dropouts, or our bikes in general? Leave it in the comment section below, or reach out to us by email any time at info@22bicycles.com.