How we finish a frame
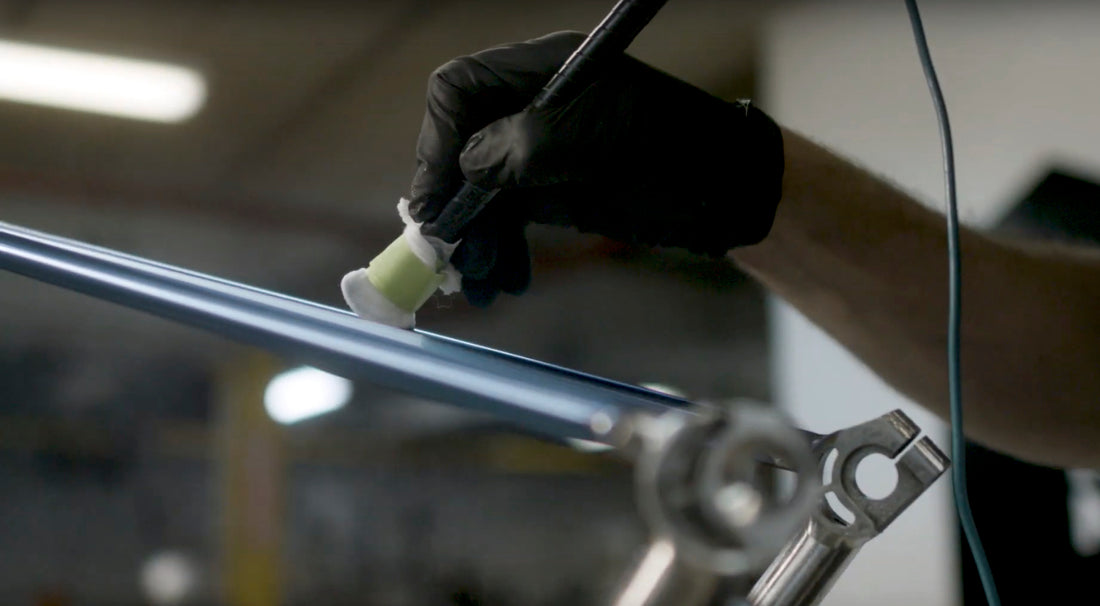
One of the final, yet defining steps that makes a No. 22 bike special is our finishing technique. When it comes to the optional anodized finishes, “There’s a little bit of magic involved,” says Scott Hock, who oversees production in our Johnstown, N.Y. factory.
The process took a lot of trial and error to perfect. Although titanium is exceptionally strong (yet light), it's also a highly demanding and fickle material. Each step, from the initial welds to blasting the finish, has to be more delicately executed than working with other frame materials.
When anodized, titanium also has a specific color spectrum. “There’s no red or black,” Hock points out, “and the gold is a bronze-yellow, which actually gets the point of the color across nicely, I think.” But Hock says that these color constraints have become a part of the No. 22 identity. “We started with a basic blue,” he says of the earliest days developing the technique. “We worked on perfecting the blue and being able to do so repetitively, then we expanded to more colours—testing different mixtures of the liquid that we use until we were able to open up the full spectrum,” There are now 10 distinctive colour options, including four unique fades which beautifully reveal the extent of the spectrum.
The process is achieved by using an electrolyte solution and running an electric current through the titanium in order to reveal a colour. Each colour on the spectrum is triggered by a specific frequency. It requires an extremely steady hand, incredible focus and years of skill.Every aspect of our design process is also done at our factory. "In order to get the logos perfect every time, we create all our decals in-house with a die-cutting machine, drafting up specific designs,” says Hock.
Hock specs four different types of vinyl, and three different types of application tape, depending on the humidity and temperature of the frame at the time. “The season actually has a big impact on how the finish reacts, so we keep a variety of materials in the shop at all times,” says Hock. And not all finishes are created equal. “A green colouring takes a day or so just to sit there and let the decal bond,” Hock points out of certain more finicky colors. High polish finishes are also tricky. “They don’t have as many microscopic grooves to adhere to the vinyl,” Hock notes.
The final step in the finishing process is blasting. “When it’s polished or anodized, the graphic is a kind of positive—that’s what we want to remain,” Hock says. It gets brought over to the blasting station and gets a thorough blasting with a material calibrated specifically for our frames. Hock actually went to a blasting materials producer in Massachusetts in order to help develop the perfect product for finishing a No. 22 frame. “We abrade it with an engineering material made out of ceramic media, which produces a much better finish than glass bead material,” he says. The high cost of the blast media is a hurdle to more widespread use, but the extra depth of the resulting finish makes that cost easy to justify.
Then, the frame is ready for its final step: being shipped to its owner.